SCOTLAND’S construction industry has been praised for its progress towards embracing a more sustainable future by one of the country’s leading resource management businesses.
Brewster Brothers recently opened a second recycling plant near Cumbernauld following the success of its Livingston operation, which has diverted 1.3 million tonnes of construction, demolition, and excavation waste from landfill over the past five years.
The company’s wash plants are used to transform the waste into high-value quality aggregates for reuse in the building trade.
Scott Brewster, MD of Brewster Brothers, explained that the firm’s growth is tangible evidence of the construction sector’s willingness to embrace new approaches, particularly around the use of recycled products. He believes there’s still some way to go, however, in terms of educating some people that recycled products are not inferior to their virgin counterparts.
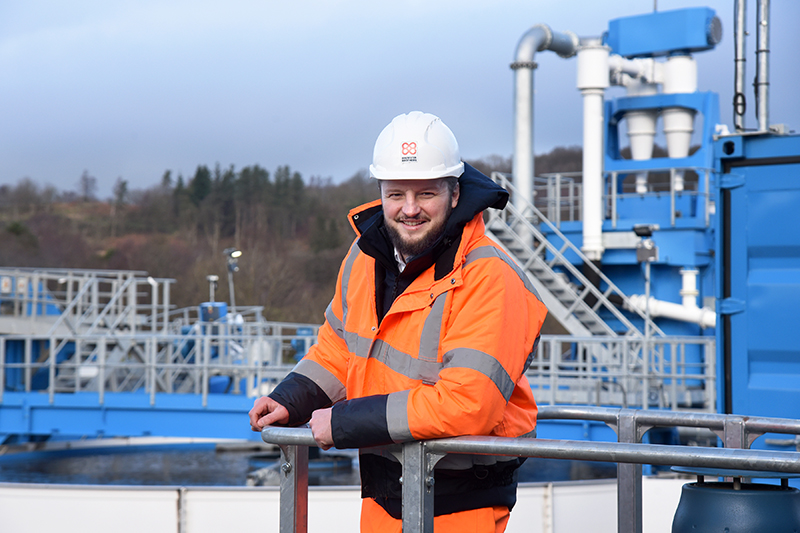
“There’s still that bit of inferiority stigma attached to them, especially when the products are coming in largely at the same price,” Scott said. “We often get push back from customers who say if it’s recycled it must be cheaper. But we’ve got higher production costs; we’ve got a brand-new plant; it’s a dirtier feed material; we’ve got additional residual waste we deal with as well compared to a virgin setting. That’s why we end up being largely competitive with virgin material as recycled aggregates are exempt from the aggregates levy and we do get a £2 per tonne head-start in a way from that.”
Brewster Brothers, which received the VIBES Circular Scotland Award in 2023, is receiving an increasing number of enquiries from main contractors and housebuilders in particular about its processes as the industry gets to grips with ambitious environmental targets. Last year the company invested a significant amount of money in obtaining a lifecycle analysis of its process, the outcome of which was an Environmental Product Declaration, which Scott revealed are becoming more popular as a benchmark to compare products from different suppliers against each other in terms of their carbon savings.
The driving force behind the new plant in Cumbernauld was the fact the Livingston site was reaching capacity. The move also gives Brewster a better spread geographically through the whole of the central belt and helps customers in the west of Scotland save on haulage costs.
When the company, which Scott founded in 2017 with his father Alex, assessed options for expansion, there were various directions it could have gone in. One option was to diversify into other waste streams. A further option was to use its own products in its own concrete production. Or, the third option, which the business settled on, was to try to replicate the success of Livingston in another part of the country.
The new site is located where the old Gartshore Brickworks used to be. The CDE wash plant installed there is capable of recycling 300,000 tonnes of waste annually and will serve construction sites, housebuilding, and utilities developments in the western central belt.
“In terms of capacity, it’s pretty much a replica of the Livingston site,” Scott added. “We’ve fitted a CFCU module, which is a counterflow classification unit. This is used in high-end sand mining, primarily to remove lignite in a virgin setting. But we’re using it to remove more of the organic content that gets caught up in the construction and demolition waste. Removing that gives a more refined product that we hope can be used in bound applications – ready-mixed concrete and asphalt. It’s a higher value product. Nationwide there’s not actually a lot of recycled content that goes into these bound products so they’re a big opportunity for us.”
Prior to Brewster Brothers’ arrival, the site was used as a film set for the global TV hit Outlander. Brewster has turned the saloon-style Western building used in the production of the show into an office.
As part of the company’s redevelopment of the derelict site, it will recycle the old bing of colliery waste and the area will be turned into a greenspace for use by the local community and to promote biodiversity.
Part of the funding – about 6.5% – for the new recycling facility came from Scottish Enterprise in the form of the Green Jobs Fund. Brewster Brothers was successful in obtaining a grant in 2021 that was conditional on attracting 15 new jobs to get the second site up and running. That has taken the company from a workforce of 27 to 42.
As with the Livingston site, the company has chosen to again partner up with CDE when it comes to the equipment.
Scott revealed, “We have a slightly different layout compared to Livingston but largely the same machinery. We have an initial oversize scalping screen. The oversize that comes off that will go into our crushing unit and will break that down to a more appropriate size. Then it comes to a pre-rinsing screen to have an initial wash and then into a more attritional process, which is the logwasher.
“That scrubs the gravel and liberates the silt and clay. The gravel comes down to a dewatering screen. That’s also a sizing screen. Meanwhile, the sand, silt and clay is still suspended in the dirty water. That goes onto the sand plant where it goes through some hydrocyclones – again taking out the silt and clay element in the wastewater. That leaves you with the sand, which falls into the CFCU tank where you have upward flow jets of water pushing the less dense material, taking that off to a trash screen, while the sand falls to the bottom of that tank and again on to a dewatering screen.
“There are two passes of that, so you get two fractions of sand – a 4mm and 2mm. The wastewater carries on to the AquaCycle, which is a clarifying tank similar to what you’d see in a sewage works. The silt and clay have a flocculant added, which clumps them together into bigger particles. They fall to the bottom through gravity and that’s ejected as a slurry into our slurry tanks while the clean wastewater is recirculated round the plant. The slurry goes into our buffer tanks and overnight is pushed up into the filter press where it is dewatered under high pressure. The cake left behind between the filter cloths drops out every hour and again the water squeezed out from that process is recycled around the plant.
“We’ve partnered with CDE again. I do call it a partnership, not just a supply arrangement. The fact we’ve gone with them for a second plant of this value speaks for itself in terms of our relationship. We’re going through training at the moment. The commissioning phase is not over yet. We’ve had a commissioning engineer with us for the whole of January. That’s just to oversee any teething issues and to train our staff.”
With sustainability becoming an increasingly prominent consideration, Scott anticipates the already competitive recycling sector becoming even larger in the coming years.
He can foresee a day when every town of a certain size will have one of these recycling facilities, stating that’s the way it should be.
“This material shouldn’t be going to landfill,” he concluded. “There’s a lot of it produced every year. For Scotland, it’s five million tonnes every year of excavation waste. For the UK as a whole it’s almost 120 million tonnes.”
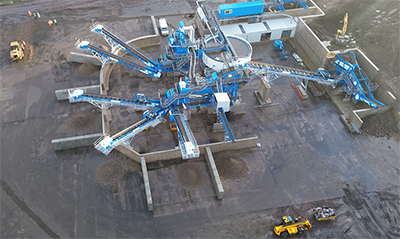