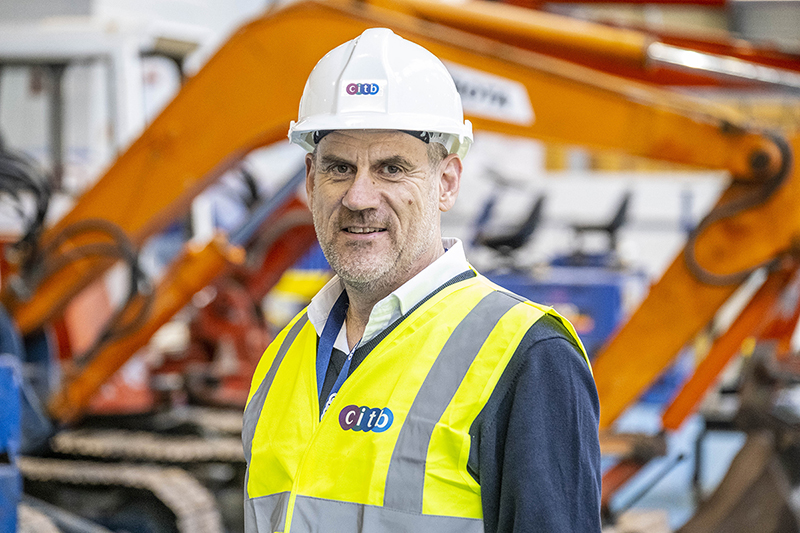
THE CITB is piloting changes across a series of plant training standards and grants in a bid to standardise training and testing requirements throughout the construction industry.
The first set of new standards have been developed in collaboration with industry working groups comprising employers, providers, and federations. The CITB said they represent a ‘real change’ in the way plant training and testing is delivered, streamlining the system and making grants more accessible.
The aim is to ensure employers see a return on their investment by producing ‘competent, work-ready’ plant operators, who have received training from experts, including learning on new technologies and the eco operation of plant.
The first phase of the changes will see new standards introduced for the following:
- Excavator 360, above 10 tonnes (tracked)
- Forward tipping dumper (wheeled)
- Rear tipping dumper/dump truck: articulated chassis (all sizes)
- Ride on roller
- Telescopic handler: all sizes excluding 360 slew
- Industrial forklift
- Plant and vehicle marshaller
- Slinger, Signaller: all types, all duties.
Alongside the new standards, the grant rates for plant training and tests will also be updated. Currently, three smaller grants are available for practical test, theory test and short course training, which employers can apply in different ways. Under the changes a single grant will be available for all CITB-registered employers.
A transition period is in place for two months, allowing employers to still receive grant for either the old or new standards while the process is embedded. After September, grants will only be available against the new requirements for the training and testing of the eight categories under review. To ensure eligibility, they will have to:
- Meet CITB’s new standards
- Lead to a card carrying the CSCS logo, and
- Be delivered by an Approved Training Organisations (ATO).
CITB explained that employers will need to provide their CITB registration number to an ATO, who will apply for the grant on their behalf. Any other plant training separate from the new standards will remain eligible for grant and employers can apply for this in the same way they currently do.
A separate, higher ‘novice’ grant rate will be available for employers who are putting staff through plant training, who have never had experience in the type of machinery they are being trained in. This is to help respond to demand for more people to become highly skilled and competent plant operators.
Peter Brown, PSRO secretariat, said, “The Plant Sector Representative Organisation (PSRO) – consisting of seven major construction plant-user federations – was set up by employers and their representative bodies to drive consistency for operational standards and certification through card schemes. Through its competency framework, the PSRO recognises the importance of the introduction of these CITB training standards and their role in ensuring high-quality and consistency of learning, coupled with robust quality assurance processes, that is required for the skills and knowledge for the safe operation of plant.”
Tim Brownbridge, academy manager at BAM Nuttall, added, “Since early in 2022 I have been involved in a voluntary industry group developing the CITB Plant Training Standards. The various plant and activity categories have been reviewed and developed by specialists with both experience and expertise relevant to the training required. The groups have been representative of all stakeholders in the use of plant from employers to trainers, owners, and operators, and I believe the end result will be of great value to industry providing a current, balanced and robust standard for training.”
Christopher Simpson, head of quality and standards at CITB, commented, “I’m delighted we have introduced these new standards, which will improve plant operations throughout England, Scotland, and Wales. These changes will help standardise and improve the quality and consistency of plant training; increase the amount of plant training that takes place before testing; and increase the number of people trained in plant operations, particularly new entrants to construction.”