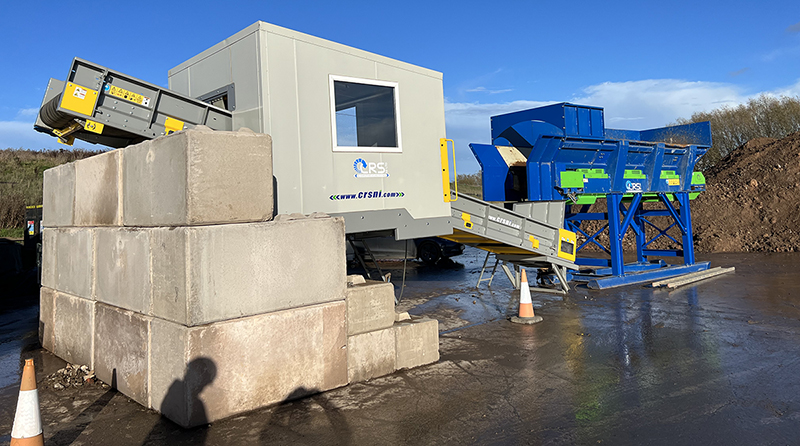
Paul Thorne, director at SCG Supplies, reflects on the evolution of recycling equipment over the past three decades
SINCE the early 1990s there’s been a constant battle to increase the amount of recycled heavy construction materials that are being reused.
The first machines I sold into recycling weren’t ballistic separators or eddy current separators; they were good old fashioned screens built for the extractives industry.
A MK2 Powerscreen and Chieftain with an 8 x 4 screenbox. That Chieftain was quite a thing then: it had its own, integral stockpile conveyors for three materials and a tipping reject grid for the big stuff. The Mark2 went to John Binks Transport (Northumberland) and the Chieftain went to work at F D Todd and Sons (North Yorkshire).
Both were local hauliers with small yards; both wanted to get into skip hire; both wanted to reuse top soil and rubble for small projects; both went on to be multi-stream waste processing and recycling operations; and both became part of big money buyouts by recycling conglomerates who were looking for opportunities in a mature, established and condensing sector.
It took a long time to get from zero to almost complete recycling but they both did it by continuing to invest in technologies as they developed.
Here’s a reminder of some words that weren’t in my (or most people’s) vocabularies in 1992: recycling; secondary aggregates; circular economy; remediation; sorting; aggregates levy; landfill tax, LOI; source segregation; waste to energy; anaerobic digestion; climate change… you get the idea!
Some of the more enlightened European countries and US states were way ahead but most people, like me, didn’t see the need to recycle or even know what it was. A few years went by and it became apparent that, despite strong reluctance from construction industry specifiers, the only really active market for screens and crushers was in recycled aggregate.
King coal was a goner and quarrying would close down the capex budget at the first sign of political or economic uncertainty. So, if progressive industries such as demolition and recycling were to convince their local clerk of works to use recycled crusher run, quality would be key.
The main arguments against re-use would be appearance and future stability of materials. If it looked like an old building left in a pile, who could blame a buyer’s reluctance at being first to use it in their flagship regeneration project?
The pro lobby would argue, correctly, that those old buildings and roads were made of better raw materials than their modern contemporaries and therefore, if properly treated, could be re manufactured into products, every bit the equal of primary aggregate.
Enter picking
During the 90s and 2000s the secondary aggregate market grew exponentially, partly through legislation but more so innovation. The products available became high-quality, cost-effective sources of sub-base and fill material. It became commonplace for skip companies and demolition contractors to look to industry colleagues in Europe for ideas.
The big idea was to remove any unwanted material from construction and demolition arisings to make them appear (and be) of suitable quality.
Metal is worth money, plastic is a fire risk as well as being unsightly, and wood is a void space waiting to happen in a crusher run construction fill.
You can blow, suck, float all you want – but in most cases human hand-eye coordination is hard to beat. After all, some stuff sinks and some floats, paper is easier to blow than a piece of wood or PVC the same size, and even a magnet isn’t infallible if the rebar it’s trying to pick up has a lump of concrete attached to it.
Pickers started on the ground which was fraught with difficulties: vehicle movements, dust, exposure to the elements, trip hazards, falling objects and the inherent lack of consistency of product when picking from an ever growing stockpile under a product conveyor.
As things developed, many contractors attempted to process material in their own yards where there could have more control of welfare and safety. Many bit the bullet and purchased static, trommel and picking cabin set-ups.
On the down side, this meant double handling and road haulage so with large proportions of finished product being retained on site, a demand grew for mobile, rapid deployment systems.
Fast forward to today and you can pretty much take all processes to the material, even on short-term contracts with limited quantities to be processed. Now, thanks to the manufacturing sector (particularly in Ireland) you can take water and air separation, mobile metal recovery (ferrous and non ferrous), shredders for wood and plastics and, of course, crushers and screens. But amongst it all, humans are the drivers behind these mobile processing sites. If you can see it coming past, well metered, uniform in size and in a mono layer, the human hand can remove it.
The current choice of mobile picking stations on the market ensures there is a safe environment for site operatives to perform the ultimate quality control on a range of waste streams, ensuring continued acceptance of materials into the circular economy.
These days 90% of hard CDW (construction and demolition waste) is recycled. Not bad going in only 30 years.
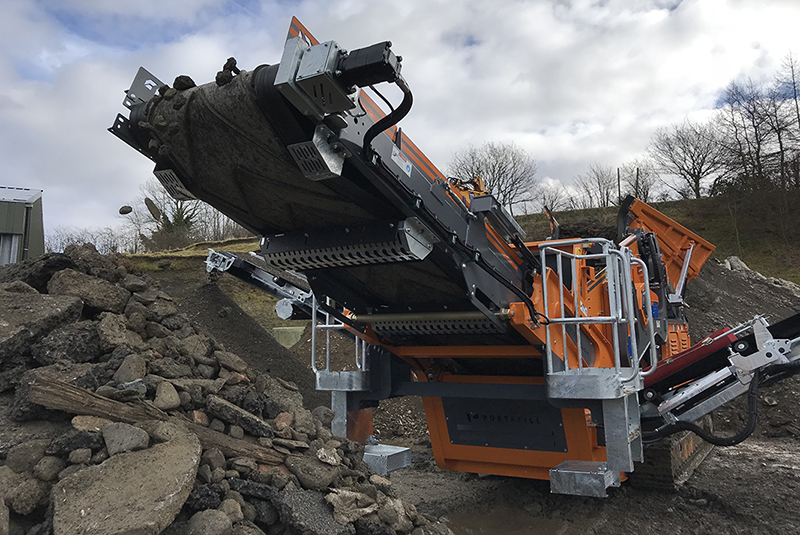