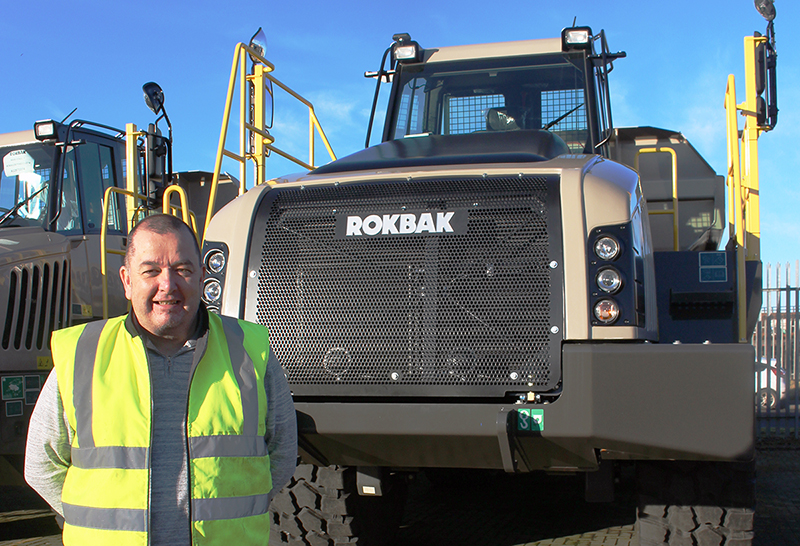
With the current economic situation, it’s more important than ever to reduce costs and achieve the lowest total cost of ownership possible. Rokbak’s senior product manager, Scott Pollock, explains how the company is helping customers achieve this.
1. A fuel-efficient drivetrain
Rokbak’s fuel-efficient drivetrains deliver powerful performance and meet worldwide emission standards with low cost of operation and low environmental impact.
Fuel consumption is the biggest cost of operating a machine. The Rokbak RA30 and RA40EU Stage V engines produce a fuel consumption saving of up to 7%, when compared to the previous EU Stage IV engines. This means lower operating costs and less impact on the environment. The RA30 EPA Tier 4 Final machines also achieved a fuel saving of up to 5% when the latest eight-speed transmission was introduced.
2. The aspirated air engine filter
A key feature towards increasing productivity and reliability for the customer is the engine air intake filter. Within the dry-type, 2-stage aspirated air cleaner, this small suction draws out major contaminates, extending the time between maintenance intervals, lowering total cost of ownership and potentially increasing machine life cycle.
3. Data-driven savings
Rokbak’s Haul Track telematics system helps machine owners to reduce total cost of ownership (TCO) by keeping an eye on everything from fuel consumption and machine usage to issues that, if neglected, could lead to repairs or unplanned downtime.
The system enables you to remotely monitor your machine to manage performance, plan preventative maintenance, proactively control production and track the condition of your hauler. By taking a deep dive into a variety of software parameters – such as travel speed, fuel consumption, temperatures and pressures – owners can look for patterns and identify improvement areas that can reduce TCO.
Haul Track connects to the onboard weighing (OBW) system, so any under or overloading can be easily identified and used to help educate operators in correct machine usage. 2022 saw the re-introduction of improved fault alerts, with improved maintenance alerts being reintroduced shortly. These not only notify the dealer of upcoming service intervals, but also provide a list of required parts for that specific task – enabling faster servicing and greater machine uptime.
4. Lengthened maintenance intervals
Both Rokbak articulated haulers are installed with hydraulic system magnetic suction filters, which reduce the risk of contaminants entering the hydraulic system, saving on disposable maintenance materials and maximising productive uptime through cleaner systems and prolonged component life.
The RA30 and RA40 both adopt modern hydraulic fluids that maximise time between maintenance periods to 4,000 hours. The RA40’s transmission has high-performance fluid and up to 6,000 hours between service intervals, while the RA30’s long-life transmission fluid supports 4,000 hours between oil maintenance intervals. As a result, customers can achieve increased productivity and uptime, as well as low cost per tonne.
5. Operator comfort = operator productivity
Rokbak has created the ideal ergonomic environment for the articulated hauler operator to work within. Operators can have a huge influence on TCO. A happy operator is a productive operator, and the more your machines move the more you earn.
Spacious, pressurised cabs have been designed to avoid fatigue and be highly comfortable – with low noise, an active air suspension operator’s seat with adjustable arm rests, cushioned steering, and high-capacity heating and air-conditioning.
The RA30 is equipped with true independent front suspension as standard, further enhancing operator comfort and enabling excellent traction control and maximum productivity, even in challenging conditions.