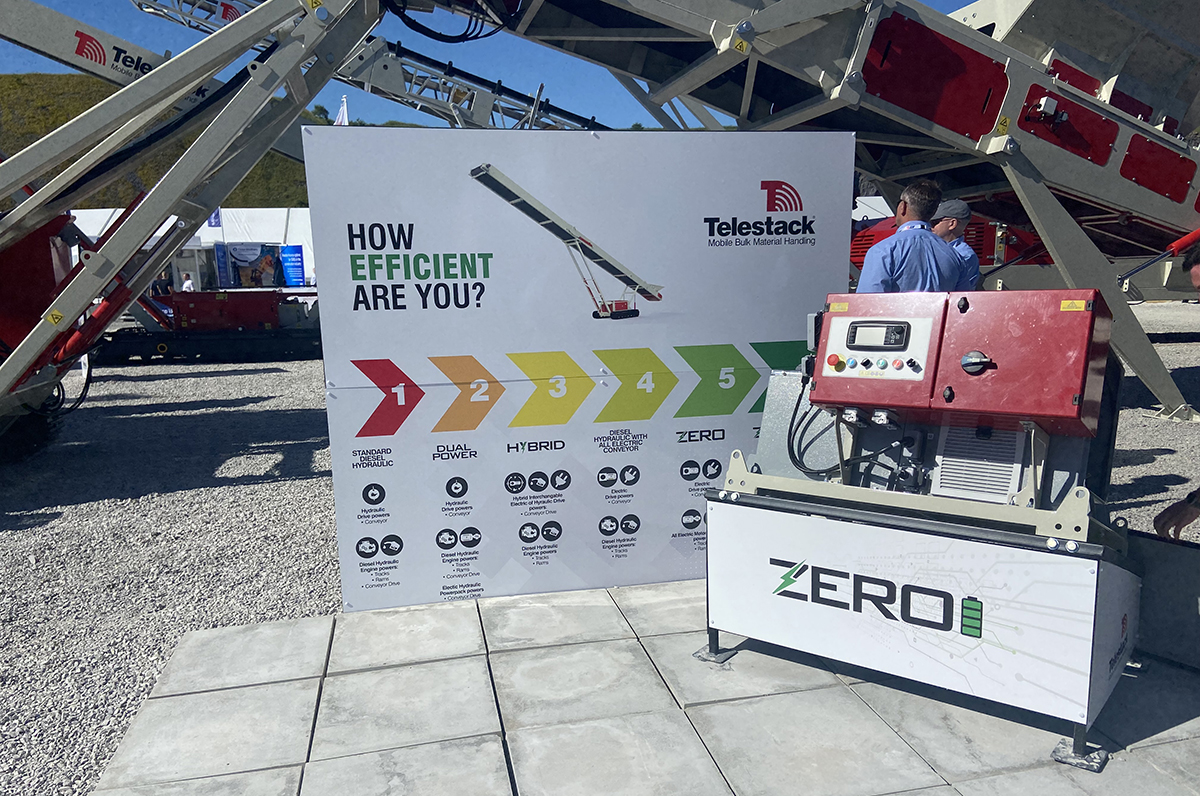
Paul Thorne, used machinery and new plant director at SCG Supplies, explains why he believes firms in the quarrying and recycling sectors are being unfairly punished when it comes to fuel, and offers some potential solutions that could be deployed to offset tax hikes
ONLOOKERS to the recycling and extractives industries would probably think everything is just fine. Most medium-sized recyclers have excellent infrastructure as you drive in; expensive concrete everywhere and of course lots of big plant and processing equipment.
Drive into a quarry or sand pit and the majority of inexperienced visitors would think they are looking at ‘free’ money being dug from the ground and sold at ever increasing rates. The reality is that there is a constant battle against all manner of hazards to businesses in these sectors.
Changing legislation seems to have been conceived and introduced with misunderstanding of the practical implications. Let’s call it what it is, in the eyes of the hard-working teams in these industries: red tape.
Health and safety challenges are everywhere too. Nothing in a quarry or transfer station is ‘people-friendly’. There are clues in the names – crusher and shredder, for example. It takes a lot of resources to ensure the safety of your team.
Then there’s road safety. You need trucks. That’s another whole article!
Recording and monitoring is another area of expertise. If you make a kilo of material – particularly recycled material – you’d better be prepared to test it, code it, name it, record what it was made from and where it’s going. And that’s all before you work out how much it cost to make.
That’s where this article really starts: how much did it cost to make?
Ex-chancellor Rishi Sunak announced 130% capital allowances in his budget statement in 2021 with the intention of getting cash-rich companies to spend on qualifying items. There is no doubt this has driven a higher-than-expected churn on plant replacement post-pandemic.
However, in the same statement he failed to address a ticking timebomb which has now started to show its effects. In 2020 the government announced its intention to introduce changes to rebated diesel and biofuels.
Businesses other than those in agriculture and fisheries would have to use white diesel to run all site equipment. So, the new shiny loading shovel or prestigious crushing plant you were encouraged to buy became an expensive liability to use overnight.
Every tonne of high quality, recycled aggregate is a tonne of the planet’s natural capacity saved and reused. Because of the advances on the recycled side of the equation, virgin material mined today enters a truly circular economy. It can and will be re-used.
Quarrying companies are also able to re-look at historical waste products such as dirt belt scalpings or fine dusts that would simply have been discarded. These are now mainstream products which slow the depletion of reserves. But they still have to use white diesel to do this.
Everyone in these industries is being unfairly penalised for stretching natural resources further than ever so that we can enjoy our easy trip to London or walk through a better built environment.
I firmly believe that there’s no one on our side in parliament because no one knows what we actually do.
Lots of companies have outreach programmes to help local communities understand the need for our industries. This is great. Can it truly educate anyone about the industry? Probably not but it increases empathy and tolerance. We can’t expect a politician to want to go to a recycling site, for example. So, when they do, they will sport the obligatory, brand new high-viz, wellies and ill-fitting hard hat. They will walk around and point at stuff they don’t want to understand and then get out of there.
What they are missing is the importance of what’s going on in this essential economic sector. Politicians focus on the new semiconductor manufacturer moving into an area; not the infrastructure that makes it possible.
Let’s look at some of the strategies that are being employed to offset this massive tax hike:
Convey the message
Recently, equipment manufacturers and processing companies have shown increasing interest in fuel efficient solutions. One of the simplest is: don’t drive a loading shovel up and down a stockpile. Aside from degradation of finished product, transmission, and tyre wear, there’s the fuel. There’s always the fuel!
An 80-foot tracked, self-powered conveyor will typically use 7-9 litres per hour of diesel. It will stockpile around 2,400 tonnes in a static position. An 18-20 tonne class latest Euro emissions-compliant loading shovel will use 16-18 litres per hour doing similar work.
Telestack unveiled their fully electric conveyor concept at Hillhead 2022. Use the battery for manoeuvring and plug the conveyor into site power or link to other machinery while working.
Some manufacturers are looking at ways to completely remove engines from the equation with the introduction of EV technology into site equipment.
Yes, you will still need to run a loading shovel; just not for the most arduous and fuel-thirsty part of the process. You may be able to use a smaller machine to load and carry or maximise the utility of an existing shovel by introducing new tasks into the workflow.
Either way, conveyors are proven to be a help with saving fuel.
Back to the future
40 years ago, companies like Parker and Pegson built crushers with electric motors running from on board generator sets to power them. At the time, progressive firms like Powerscreen were perfecting simple diesel/hydraulic systems to drive their machines. The swing to diesel/hydraulic was embraced universally as simpler and safer. We lived in a world, unlike now, where the efficiency of equipment was not a prime consideration. Get the big production first and ask questions later.
This was an age when waste to landfill peaked, resources seemed infinite, there was no UK recycling industry to speak of, and the term global warming hadn’t been invented.
A few companies such as Doppstadt and Kleeman still offered the plug in or gen set option because, perhaps in Germany and Holland, the yard and factory-based recycling industry was growing rapidly ahead of ours.
Well, we’ve come full circle it seems. In a mature and sophisticated market like the UK today, manufacturers have to offer electric, dual power hybrid and diesel/hydraulic versions of the same piece of kit.
You can see on the factory floor at Portafill International that increasing numbers of machines are being prepped to receive the operators’ site power. In one recent case, a machine was being used to feed a recycled aggregate washing plant that had a generator powering it, so it seemed inefficient to run two engines. Once unplugged however, these machines are free to roam and process under their own diesel power.
In a market where fuel levies are having to be placed on each tonne of material in some cases and interest rates are climbing, the ‘B word’ and global supply chain issues leading to extended delivery time on plant, using white diesel to run processing equipment, to make every road and building in the UK, is yet another sign of just how far business and politics are apart.
One thing you can rely on is that Screening Valley (as the manufacturing belt of the North of Ireland is nicknamed) will keep pushing the R&D spend to keep bringing the latest efficiencies to customers in Scotland and worldwide.